A króm-karbid egy kerámiavegyület, amely többféle kémiai összetételben létezik: Cr3 C2, Cr7 C3 és Cr23 C6. Normál körülmények között szürkeállományként létezik. A króm nagyon kemény és korrózióálló fém. Ezenkívül égésgátló, ami azt jelenti, hogy még magas hőmérsékleten is erős marad.
A króm ezen tulajdonságai miatt fémötvözetek adalékanyagaként használható. Ha keményfém kristályokat építenek be az anyag felületébe, az javítja a kopásállóságot és a korrózióállóságot, és megőrzi ezeket a tulajdonságokat magasabb hőmérsékleten is. A legösszetettebb és leggyakrabban használt vegyület erre a célra a Cr3 C2.
A rokon ásványok közé tartozik a tongbaite és az izovit (Cr, Fe) 23 C6, mindkettő rendkívül ritka. Egy másik gazdag karbid ásvány a jarlongit Cr4 Fe4 NiC4.
Chromium-tulajdonságok
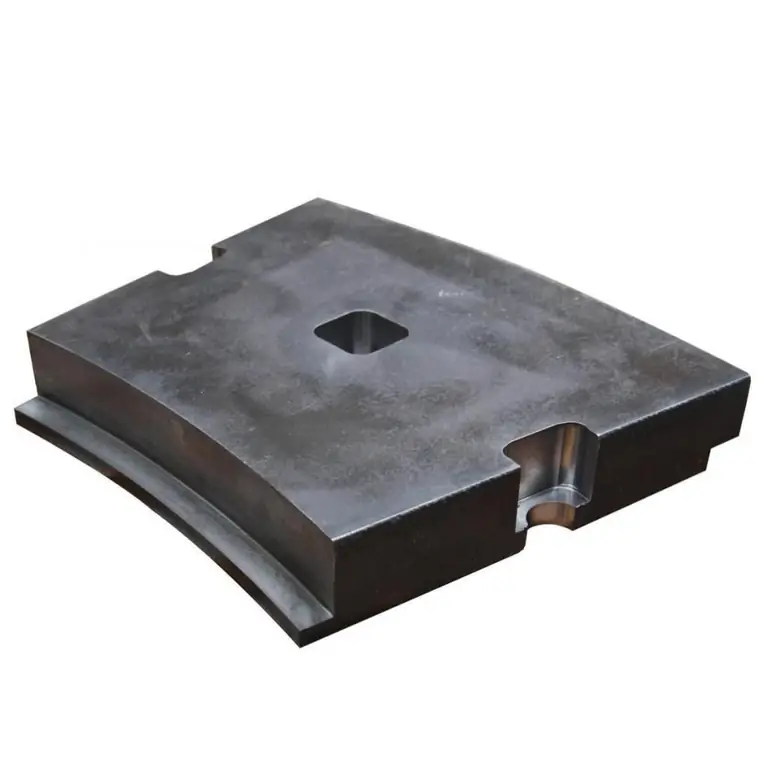
Vannakhárom különböző kristályszerkezet a karbidhoz, amelyek három különböző kémiai összetételnek felelnek meg:
- Cr23 C6 köbös szerkezetű, Vickers-keménysége pedig 976 kg/mm2. A
- Cr7 C3 hatszögletű kristályszerkezettel rendelkezik, mikrokeménysége pedig 1336 kg/mm2. A
- Cr3 C2 a három összetétel közül a legtartósabb, rombusz alakú szerkezete, mikrokeménysége 2280 kg/mm2.
Ezért a Cr3 C2 a felületkezelésben használt króm-karbid fő képlete.
Szintézis
A keményfém kötés mechanikus ötvözéssel érhető el. Az ilyen típusú eljárás során a fémkrómot és a grafit formájában lévő szenet egy golyósmalomba táplálják, és finom porrá őrlik. A komponensek összezúzása után granulátummá egyesítik és forró izosztatikus préselésnek vetik alá. Ez a művelet inert gázt, elsősorban argont használ, zárt sütőben.
Ez a nyomás alatt álló anyag minden oldalról nyomást gyakorol a mintára, miközben a sütő felmelegszik. A hő és a nyomás hatására a grafit és a fém reakcióba lép egymással, és króm-karbidot képez. A szén százalékos arányának csökkenése a kezdeti keverékben a Cr7 C3 és Cr23 C6 formák hozamának növekedéséhez vezet.
A króm-karbid szintézisének másik módszere oxidot, tiszta alumíniumot és grafitot használ egy önterjedő exoterm reakcióban, amely a következőképpen megy végbe:
3Cr2O3 + 6Al + 4C → 2Cr3C2 + 3Al 2O3
Ennél a módszernél a reagensekösszetörjük és golyósmalomban összekeverjük. Az egységes port ezután tablettává préseljük, és inert argonatmoszférába helyezzük. A mintát ezután felmelegítjük. Forró huzal, szikra, lézer vagy sütő adhat hőt. Exoterm reakció indul be, és a keletkező gőz szétteríti a hatást a minta többi részében.
Króm-karbidok gyártása
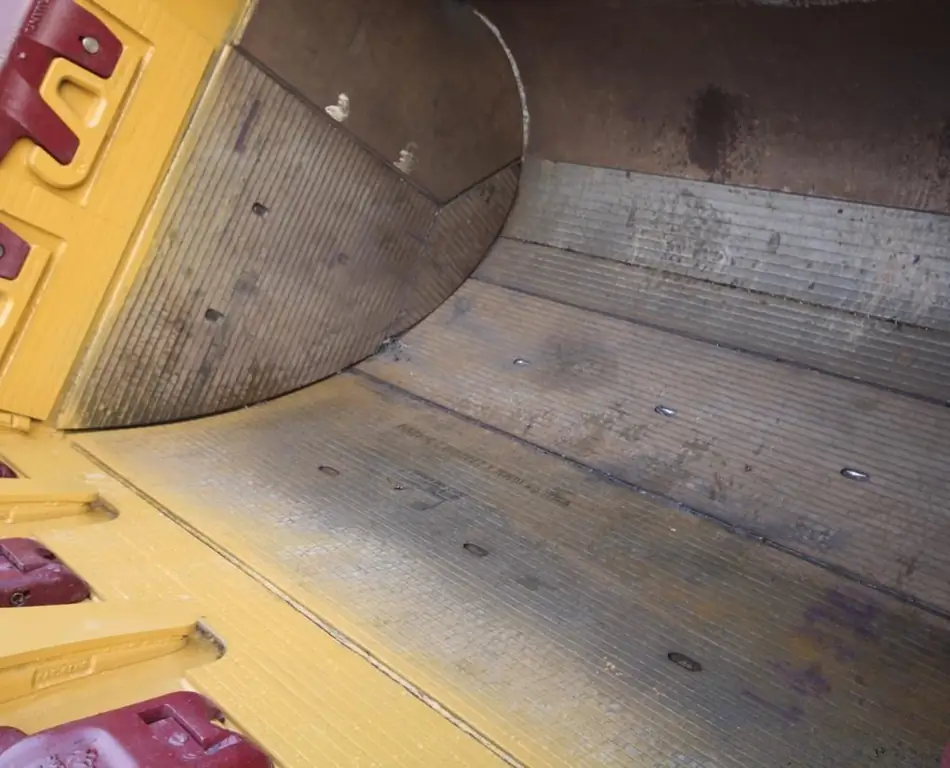
Sok cég állítja elő az anyagot az alumíniumtermikus redukció és a vákuumfeldolgozás kombinálásával 1500°C-os és magasabb hőmérsékleten. Fém króm, oxid és szén keverékét készítik elő, majd vákuumkemencébe töltik. A sütő nyomását csökkentjük, és a hőmérsékletet 1500 °C-ra emeljük. A szén ezután reakcióba lép az oxiddal fém- és gáz-monoxidot képezve, amelyet vákuumszivattyúkba vezetnek. A króm ezután a maradék szénnel egyesül, és karbidot képez.
Az összetevők közötti pontos egyensúly határozza meg a kapott anyag tartalmát. Ezt gondosan ellenőrzik annak biztosítása érdekében, hogy a termék minősége megfeleljen az olyan igényes piacoknak, mint az űrhajózás.
Fémes króm gyártása
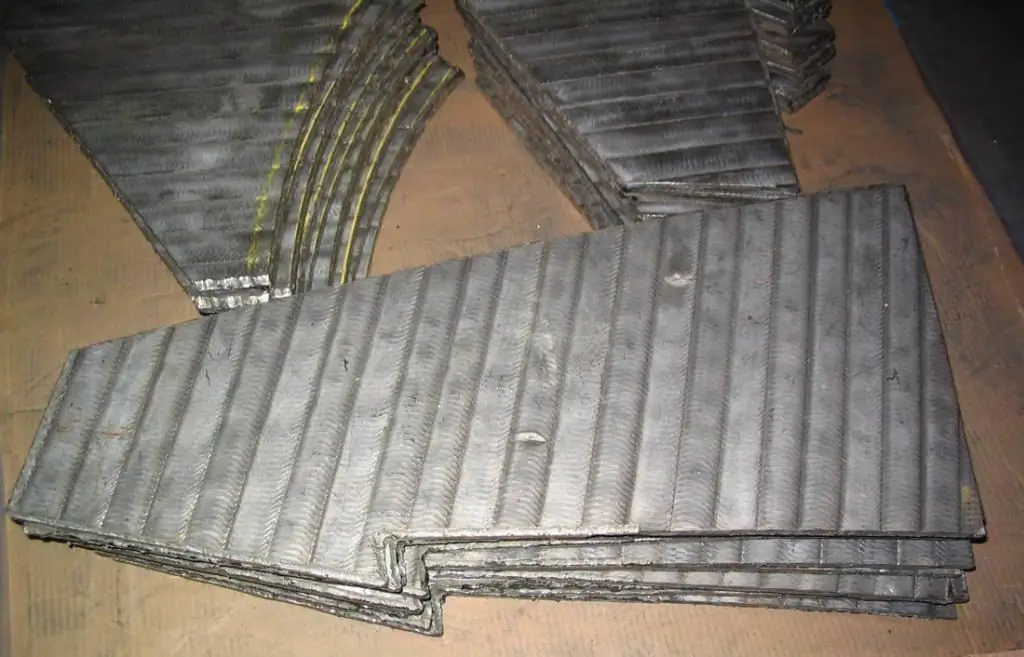
- A kutatók a karbidok új osztályát fedezték fel, amelyek stabilitása egy rendezetlen szerkezetből származik.
- A tanulmány eredményei megalapozzák a gyakorlati alkalmazásokban hasznos új karbidok jövőbeni felméréseit.
- A 2D nitridek létrehozása most egyszerűbb lett.
Fém azsok cégnél alkalmazzák, aluminoterm redukcióval állítják elő, ahol króm-oxid és alumíniumpor keveréke keletkezik. Ezután egy pörkölőedénybe töltik, ahol a keveréket meggyújtják. Az alumínium 2000-2500°C hőmérsékleten redukálja a króm-oxidot fémmé és alumínium-oxid-salakká. Ez az anyag olvadékmedencét képez az égetőkamra alján, ahol a hőmérséklet kellően leesése után összegyűjthető. Ellenkező esetben a kapcsolatfelvétel nehéz és nagyon veszélyes lesz. Ezután a kiindulási anyagot porrá alakítják, és nyersanyagként használják fel a króm-karbid előállításához.
További csiszolás
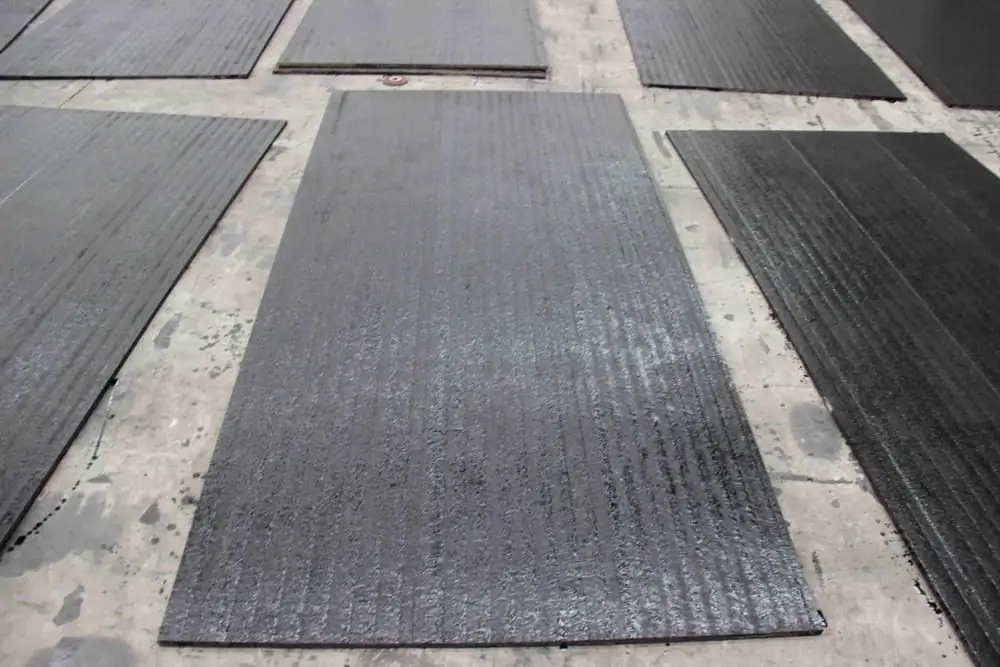
A króm-karbid és kiindulási anyaga aprítása malomban történik. Finom fémpor őrlésekor mindig fennáll a robbanásveszély. Ezért a malmokat kifejezetten az ilyen lehetséges veszélyek kezelésére tervezték. Kriogén hűtést (leggyakrabban folyékony nitrogént) is alkalmaznak a létesítményben az őrlés megkönnyítésére.
Kopásálló bevonatok
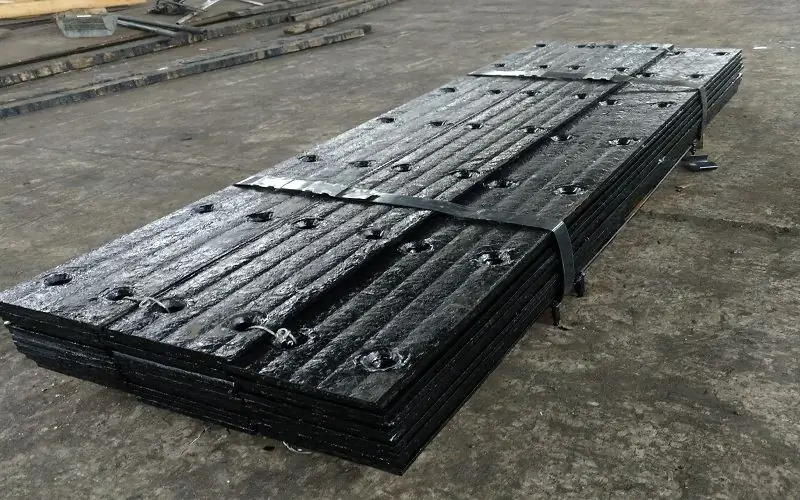
A karbidok kemények, ezért a króm általános felhasználása az, hogy erős kopásálló bevonatot képezzenek a védendő alkatrészeken. Védőfém mátrixszal kombinálva könnyen felvihető és költséghatékony korróziógátló és kopásálló szerek is kifejleszthetők. Ezeket a bevonatokat hegesztéssel vagy termikus szórással készítik. Más ellenálló anyagokkal kombinálva a króm-karbid használhatóformáló vágószerszámok.
Hegesztőelektródák
Ezeket a króm-karbid rudakat egyre gyakrabban használják a régi ferrokróm- vagy széntartalmú alkatrészek helyett. Kiváló és következetesebb eredményeket adnak. Ezekben a hegesztőelektródákban a kötési folyamat során króm-II-karbid keletkezik, hogy kopóréteget képezzen. A karbidok képződését azonban a kész hézag pontos körülményei határozzák meg. Ezért előfordulhatnak köztük olyan változások, amelyek a króm-karbidot tartalmazó elektródáknál nem láthatók. Ez a lerakódott hegesztés kopásállóságában is megmutatkozik.
Száraz homokgumiból készült kerék tesztelésekor azt találták, hogy a ferrokróm- vagy szénelektródákra alkalmazott vegyület kopási aránya 250%-kal magasabb. A króm-karbidhoz képest.
A hegesztőiparban a pálcás elektródáktól a fluxusos huzalokig terjedő trend az anyag javára válik. A porított elemben szinte kizárólag króm-karbidot használnak a nagy széntartalmú ferrokróm helyett, mert nem szenved a benne lévő vasfelesleg okozta hígító hatástól.
Ez azt jelenti, hogy nagyobb mennyiségű kemény részecskét tartalmazó bevonat nyerhető, amely nagy kopásállósággal rendelkezik. Ezért, mivel az automatizálás előnyei és az utóbbi anyaghegesztési technológiához kapcsolódó nagyobb termelékenység miatt a rúdelektródákról a fluxusos huzalra való áttérés történik, a keményfém piac növekszik.
Tipikus felhasználási területa következők: szállítószalag csavarok, üzemanyag-keverő lapátok, szivattyú járókerekek keményítése és általános króm alkalmazások, ahol kopásállóság szükséges.
Hőspray
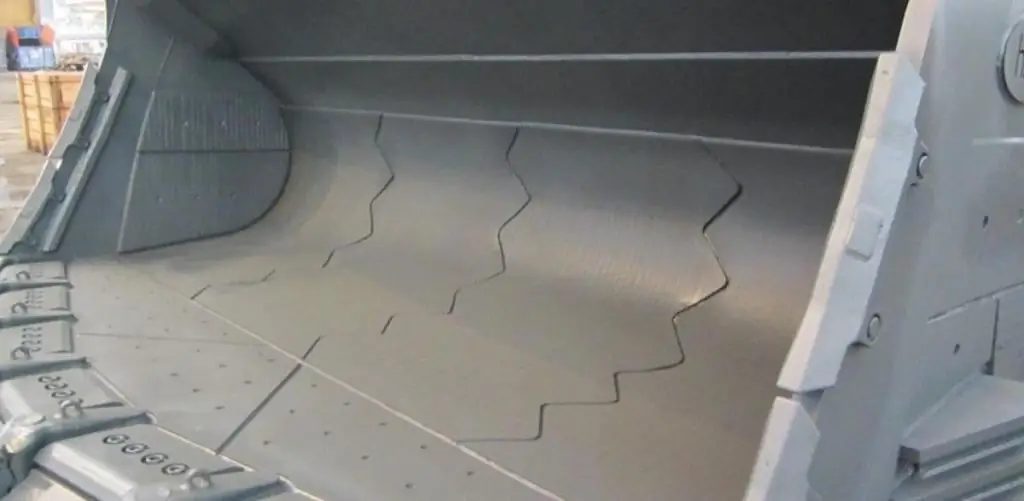
Hőpermetezéskor a króm-karbidot fémmátrixszal, például nikkel-krómmal kombinálják. Ezeknek az anyagoknak az aránya jellemzően 3:1, ill. Egy fém mátrix van jelen, amely a karbidot a bevont hordozóhoz köti, és magas fokú korrózióállóságot biztosít.
E tulajdonság és a kopásállóság kombinációja azt jelenti, hogy a termikusan szórt CrC-NiCr bevonatok alkalmasak magas hőmérsékletű kopásgátlóként. Ez az oka annak, hogy egyre gyakrabban használják őket a repülőgép-piacon. Tipikus alkalmazási terület a rúdtüskék, melegsajtoló szerszámok, hidraulikus szelepek, gépalkatrészek, alumínium alkatrészek kopásvédelme és általános alkalmazások, amelyek jó korrózió- és kopásállóságot biztosítanak 700-800°C-ig.
A krómozás alternatívája
Új alkalmazás termikusan szórt bevonatokhoz a kemény termék telítettségének helyettesítésére. A kemény krómozás jó felületi minőséggel, alacsony költséggel kopásálló héjat eredményez. A krómozást úgy érik el, hogy a telítendő tárgyat krómot tartalmazó vegyi oldatot tartalmazó tartályba mártják. Ezután elektromos áram folyik át a tartályon, amitől az anyag lerakódik az alkatrészekre éskoherens bevonat kialakítása. Mindazonáltal növekvő környezetvédelmi aggályok kapcsolódnak a használt galvanizáló oldatból származó szennyvíz ártalmatlanításához, és ezek a problémák az eljárás költségeinek növekedését okozták.
A króm-karbid bevonatok kopásállósága két és fél-ötször jobb, mint a keménykrómozás, és nincs szennyvízelvezetési probléma. Ezért egyre gyakrabban használják kemény krómozásra, különösen akkor, ha fontos a kopásállóság, vagy ha nagy részhez vastag bevonat szükséges. Ez egy érdekes és gyorsan növekvő terület, amely egyre fontosabb lesz, ahogy a környezetvédelmi megfelelés költségei nőnek.
Vágószerszámok
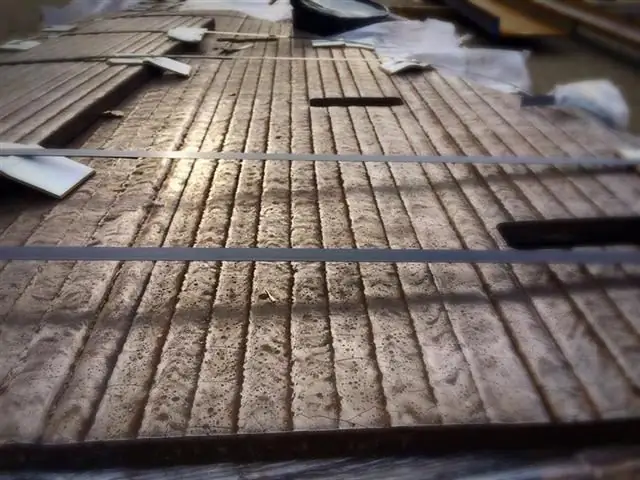
Az uralkodó anyag a volfrám-karbid por, amelyet kob alttal szintereznek, hogy rendkívül kemény tárgyakat állítsanak elő. A vágószerszámok szívósságának javítása érdekében titán-, nióbium- és króm-karbidot adnak az anyaghoz. Utóbbinak az a szerepe, hogy a szinterezés során megakadályozza a szemek növekedését. Ellenkező esetben a folyamat során túl nagy kristályok képződnek, amelyek ronthatják a vágószerszám szívósságát.