A bronz egy réz alapú ötvözet. Segédfémek lehetnek nikkel, cink, ón, alumínium és mások. Ebben a cikkben megvizsgáljuk a típusokat, technológiai jellemzőket, vegyi anyagokat. a bronz összetétele, valamint gyártási módjai.
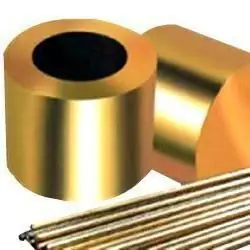
Osztályozás
1. A kémiai összetétel szerint ezt a fémet általában két csoportra osztják. Az első az ónbronzok. Ezekben az ón a fő ötvözőelem. A második ónmentes. Erről az alábbiakban részletesebben fogunk beszélni.
2. A bronz technológiai sajátosságai szerint deformálható és öntödeire szokás osztani. Az előbbiek nyomás alatt jól feldolgozhatók. Ez utóbbiakat alakos öntvényekhez használják.
Ez a fém a sárgarézhez képest sokkal jobb súrlódásgátlóval, mechanikai tulajdonságokkal és korrózióállósággal rendelkezik. Valójában a bronz réz és ón (mint fő segédelem) ötvözete. Itt nem a nikkel és a cink a fő ötvözőelemek, ehhez olyan összetevőket használnak, mint az alumínium, ón, mangán, szilícium, ólom, vas, berillium, króm, foszfor, magnézium, cirkónium és mások.
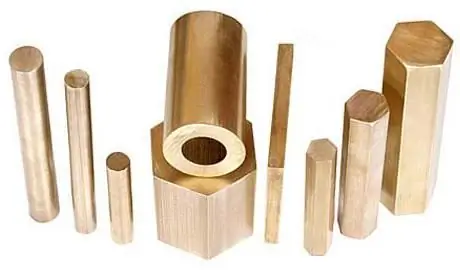
Ónbronzok: Öntöde
Nézzük ki, mi az ilyen fém. Az ónbronz (az alábbi képen öntött alkatrészek láthatók) olyan ötvözet, amelynek folyékonysága alacsonyabb, mint más típusok. Azonban jelentéktelen térfogati zsugorodása van, ami lehetővé teszi formázott bronzöntvények előállítását. Ezek a tulajdonságok határozzák meg a bronz aktív felhasználását a súrlódásgátló alkatrészek öntésében. A szóban forgó ötvözetet vizes közegben (beleértve a tengervizet is) vagy vízgőzben, olajokban és nagy nyomáson történő működésre szánt szerelvények gyártásához használják. Felelősségteljes célokra léteznek úgynevezett nem szabványos öntőbronzok is. Csapágyak, fogaskerekek, perselyek, szivattyúalkatrészek, tömítőgyűrűk gyártására használják. Ezeket az alkatrészeket úgy tervezték, hogy nagy nyomáson, nagy sebességen és alacsony terhelés mellett működjenek.
Ólombronzok
Az öntödei ónötvözetek ezen alfaját csapágyak, tömítések és formázott öntvények gyártására használják. Az ilyen bronzokat alacsony mechanikai tulajdonságok jellemzik, aminek eredményeként a csapágyak és perselyek gyártása során egyszerűen egy acél alapra helyezik őket nagyon vékony réteg formájában. A magas óntartalmú ötvözetek mechanikai tulajdonságai magasabbak. Ezért acél hátlap nélkül is használhatók.

Ónbronzok: deformálható
A nyomással feldolgozott ötvözetek általában a következő csoportokba sorolhatók:ón-foszfor, ón-cink és ón-cink-ólom. Alkalmazásukat a cellulóz- és papíriparban (hálók készülnek belőlük) és a gépészetben (rugók, csapágyak, gépalkatrészek gyártása) találták meg. Ezenkívül ezeket az anyagokat bimetál termékek, rudak, szalagok, szalagok, fogaskerekek, fogaskerekek, perselyek és tömítések nagy terhelésű gépekhez, műszercsövek, nyomórugók gyártásához használják. Az elektrotechnikában a bronz (kovácsolt) elterjedtsége kiváló mechanikai tulajdonságainak köszönhető (a magas elektromos jellemzőkkel együtt). Áramvezető rugók, dugaszolható csatlakozók, érintkezők gyártására használják. A vegyiparban az ónbronzokból rugóhuzalokat, a precíziós mechanikában - szerelvényeket, a papíriparban - kaparókat, az autó- és traktoriparban - perselyeket és csapágyakat gyártanak.
Ezek az ötvözetek extra kemény, kemény, félkemény és lágy (lágyított) állapotban szállíthatók. Az ónbronzokat általában hidegen megmunkálják (hengerelték vagy húzzák). A forró fémet csak préselik. Nyomás alatt a bronz tökéletesen megmunkálható hidegen és melegen egyaránt.
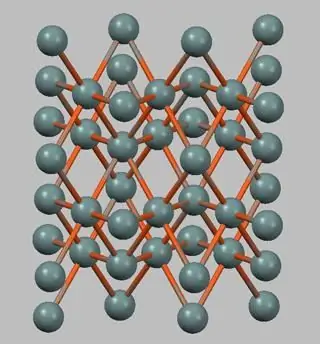
Berillium bronz
Ez a csapadékban keményedő fémek csoportjába tartozó ötvözet. Magas mechanikai, fizikai és rugalmas tulajdonságokkal rendelkezik. A berillium bronz magas hőállósággal, korrózióállósággal és ciklikus szilárdsággal rendelkezik. Alacsonynak ellenállhőmérséklet, nem mágnesez, és ütéskor nem ad szikrát. A berillium bronzok keményítése 750-790 Celsius fokos hőmérsékleten történik. A kob alt, vas és nikkel hozzáadása hozzájárul a hőkezelés során a fázisátalakulások sebességének lassításához, ami nagyban megkönnyíti az öregedés és a keményedés technológiáját. Ezenkívül a nikkel hozzáadása hozzájárul az átkristályosítási hőmérséklet növekedéséhez, és a mangán helyettesítheti, bár nem teljesen, a drága berilliumot. A bronz fenti jellemzői lehetővé teszik ennek az ötvözetnek a rugók, rugóalkatrészek és membránok gyártásában való felhasználását az óraiparban.
Réz és mangán ötvözete
Ez a bronz különlegesen magas mechanikai tulajdonságokkal rendelkezik. Hidegen és melegen is nyomással dolgozzák fel. Ezt a fémet nagy hőállóság, valamint korrózióállóság jellemzi. A mangán hozzáadásával készült rézötvözet széles körben alkalmazható kemenceszerelvényekben.
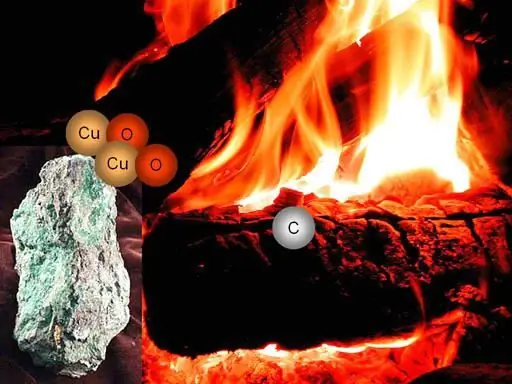
Szilícium bronz
Ez egy nikkelt, ritkábban mangánt tartalmazó ötvözet. Az ilyen fémet rendkívül magas mechanikai, súrlódásgátló és rugalmas tulajdonságok jellemzik. Ugyanakkor a szilíciumbronz alacsony hőmérsékleten sem veszíti el plaszticitását. Az ötvözet jól forrasztható, nyomással feldolgozható mind magas, mind alacsony hőmérsékleten. A kérdéses fém nem mágnesezett, ütéskor nem szikrázik. Ez magyarázza a bronz (szilícium) széles körben elterjedt használatát a tengeri hajógyártásban a súrlódásgátló alkatrészek, csapágyak, rugók,rácsok, elpárologtatók, hálók és vezetőperselyek.
Ónmentes ötvözetek öntése
Ezt a bronztípust jó korrózió, súrlódásgátló tulajdonságok, valamint nagy szilárdság jellemzi. Olyan alkatrészek gyártására használják, amelyeket különösen nehéz körülmények között üzemeltetnek. Ide tartoznak a fogaskerekek, szelepek, perselyek, nagy teljesítményű turbinákhoz és darukhoz való fogaskerekek, edzett acél alkatrészekkel párhuzamosan működő csigacsigák, nagy nyomású és lökésterhelés alatt működő csapágyak.
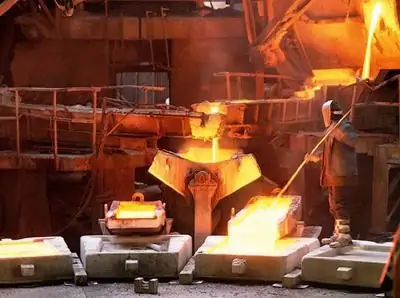
Hogyan készítsünk bronzot?
E fém előállítását speciális, rézötvözetek olvasztására használt kemencékben kell végezni. Bronztöltés készülhet friss fémekből vagy másodlagos hulladék hozzáadásával. Az olvasztási folyamatot általában folyósító vagy faszénréteg alatt hajtják végre.
A friss fémek töltetével végzett folyamat egy bizonyos sorrendben megy végbe. Először a szükséges mennyiségű folyósítószert vagy szenet egy erősen fűtött kemencébe töltik. Ezután rezet helyeznek oda. Miután megvárta, amíg megolvad, növelje a fűtési hőmérsékletet 1170 fokra. Ezt követően az olvadékot deoxidálni kell, amihez foszforrezet adnak hozzá. Ez a folyamat két szakaszban hajtható végre: közvetlenül a kemencében, majd az üstben. Ebben az esetben az adalékanyagot egyenlő arányban adagoljuk. Ezután hozzáadjuk az olvadékhoz a szükséges 120 fokra melegített ötvözőelemeket. A tűzálló komponenseket ligatúrák formájában kell bevinni. További olvadt bronz (fotó,alább, az olvasztási folyamatot mutatja be) addig keverjük, amíg az összes hozzáadott anyag teljesen fel nem oldódik, és a kívánt hőmérsékletre melegítjük. A keletkező ötvözet kemencéből történő kibocsátásakor öntés előtt a maradék (50%) foszforrézzel véglegesen deoxidálni kell. Ez azért történik, hogy bronzot szabadítson fel az oxidokból, és növelje az olvadék folyékonyságát.
Olvasztás újrahasznosított anyagokból
Annak érdekében, hogy bronzot újrahasznosított fémekből és hulladékból készítsenek, az olvasztást a következő sorrendben kell elvégezni. Először a rezet megolvasztják és foszfor-adalékokkal deoxidálják. Ezután keringő anyagokat adnak az olvadékhoz. Ezt követően a fémek teljesen megolvadnak, és az ötvözőelemeket a megfelelő sorrendben vezetik be. Abban az esetben, ha a töltet kis mennyiségű tiszta rézből áll, először meg kell olvasztani a keringő fémeket, majd hozzáadni kell a rezet és az ötvözőelemeket. Az olvasztást folyósító vagy faszénréteg alatt végezzük.
A keverék megolvasztása és a kívánt hőmérsékletre való melegítése után megtörténik a keverék végső deoxidációja foszforrézzel. Ezután az olvadékot kalcinált szénnel vagy szárított fluxussal fedjük le. Utóbbi fogyasztása a fém 2-3 tömegszázaléka. A felforrósított olvadékot 20-30 percig tartjuk, időszakonként keverjük, majd a levált salakot eltávolítjuk a felületéről. Minden, bronz készen áll az öntésre. A jobb salakeltávolítás érdekében az üstbe kvarchomok kerülhet, ami besűríti azt. Annak meghatározására, hogy a bronz készen áll-e a formákba öntésre, egy speciálistechnológiai teszt. Az ilyen minta törésének egyenletesnek és tisztának kell lennie.
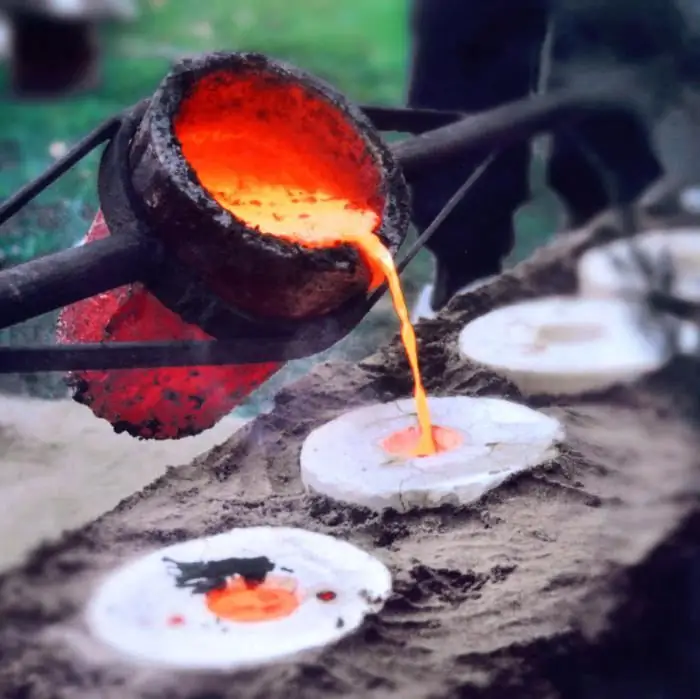
Alumíniumbronz
Réz és alumínium ötvözete, mint ötvözőelem. Ennek a fémnek az olvadási folyamata jelentősen eltér a fentiektől, amit a segédkomponens kémiai jellemzői magyaráznak. Fontolja meg, hogyan készítsen bronzot alumíniumötvözet alkatrészekből. Az ilyen típusú ötvözetek újrahasznosított anyagok felhasználásával történő gyártása során a foszforkomponensekkel végzett deoxidációt nem használják. Ez annak a ténynek köszönhető, hogy a foszfort alacsonyabb affinitás jellemzi az oxigénmolekulákhoz, mint az alumíniumot. Azt is tudni kell, hogy ez a fajta bronz nagyon érzékeny a túlmelegedésre, ezért a hőmérséklet nem haladhatja meg az 1200 fokot. Túlhevített állapotban az alumínium oxidálódik, és a bronzötvözet gázokkal telítődik. Ezen túlmenően az ilyen típusú bronz olvasztásakor keletkező oxid nem redukálódik deoxidálószerek hozzáadásával, és nagyon nehéz eltávolítani az olvadékból. Az oxidfilmnek nagyon magas olvadáspontja van, ami jelentősen csökkenti a bronz folyékonyságát és kilökődést okoz. Az olvasztás nagyon intenzíven, a fűtési hőmérséklet felső határán történik. Ezenkívül a kész olvadékot nem szabad a kemencében tartani. Alumíniumbronz olvasztásakor fedőrétegként 50% szóda és 50% kriolit folyasztószer használata javasolt.
A kész olvadékot formákba öntés előtt finomítják mangán-klorid hozzáadásával, ill.cink-klorid (a töltet teljes tömegének 0,2-0,4%-a). Ezt az eljárást követően az ötvözetet öt percig kell tartani a gázfejlődés teljes leállásáig. Ezt követően a keveréket a kívánt hőmérsékletre melegítjük és formákba öntjük.
A magas (50-60%) ólomszennyeződést tartalmazó bronzolvadék szegregációjának elkerülése érdekében javasolt 2-2,3% nikkel hozzáadása réz-nikkel ligatúrák formájában. Vagy folyasztószerként alkálifém-szulfát sót kell használni. Nikkelt, ezüstöt, mangánt, ha ezek a bronz részei, az ónadalékolási eljárás előtt kell az olvadékba bevinni. Ezenkívül a kapott ötvözet minőségének javítása érdekében néha tűzálló fémeken alapuló kisebb adalékokkal módosítják.