A korróziós sebesség egy többtényezős paraméter, amely mind a külső környezeti feltételektől, mind az anyag belső tulajdonságaitól függ. A normatív és műszaki dokumentációban bizonyos korlátozások vannak a fémroncsolás megengedett értékeire vonatkozóan a berendezések és épületszerkezetek üzemeltetése során, hogy biztosítsák azok problémamentes működését. A mérnöki területen nincs univerzális módszer a korróziós sebesség meghatározására. Ennek oka az összes tényező figyelembevételének összetettsége. A legmegbízhatóbb módszer a létesítmény működési történetének tanulmányozása.
Criteria
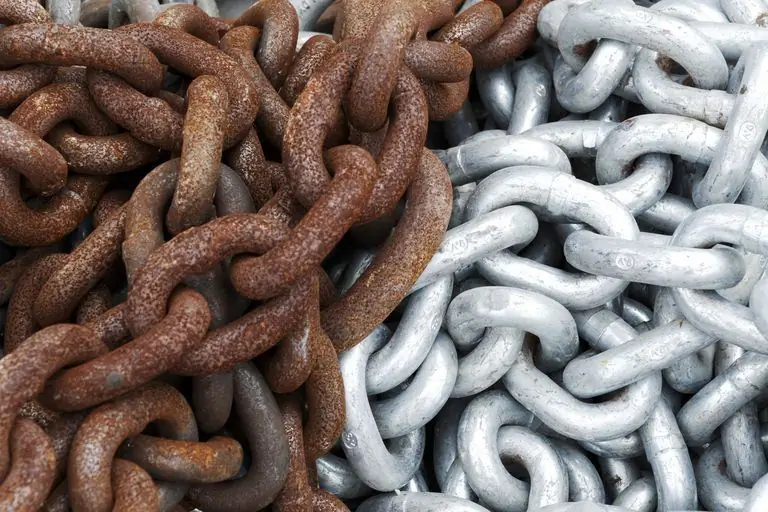
Jelenleg többféle korróziós arányt alkalmaznak a műszaki tervezésben:
- Közvetlen értékelési módszer szerint: egy fémalkatrész tömegének csökkenése felületegységenként - tömegjelző (gramm/1 m2 1 órán keresztül); sérülési mélység (vagy korróziós folyamatáteresztő képesség), mm/év; a korróziós termékek felszabaduló gázfázisának mennyisége; az az időtartam, amely alatt az első korróziós sérülés megjelenik; a korróziós központok száma egységnyi területenfelületek, amelyek egy bizonyos idő alatt jelentek meg.
- Közvetetten becsült: elektrokémiai korróziós áramerősség; elektromos ellenállás; a fizikai és mechanikai jellemzők megváltozása.
Az első közvetlen értékelési mutató a leggyakoribb.
Számítási képletek
Általános esetben a fém korróziós sebességét meghatározó súlyveszteséget a következő képlettel határozzuk meg:
Vkp=q/(St), ahol q a fém tömegének csökkenése, g;
S - felület, amelyről az anyagot átvitték, m2;
t - időszak, óra
Fémlemez és a belőle készült héjak esetében határozza meg a mélységi indexet (mm/év):
H=m/t, m a fémbe való behatolás mélysége.
A következő összefüggés van a fent leírt első és második mutató között:
H=8, 76Vkp/ρ, ahol ρ az anyag sűrűsége.
A korróziós sebességet befolyásoló fő tényezők
A következő tényezők csoportjai befolyásolják a fémpusztulás mértékét:
- belső, az anyag fizikai és kémiai természetéhez kapcsolódóan (fázisszerkezet, kémiai összetétel, az alkatrész felületi érdessége, az anyagban lévő maradék és üzemi feszültségek és egyebek);
- külső (környezeti feltételek, korrozív közeg mozgási sebessége, hőmérséklet, a légkör összetétele, inhibitorok vagy stimulánsok jelenléte és mások);
- mechanikai (korróziós repedések kialakulása, fém roncsolódása ciklikus terhelés hatására,kavitáció és korrózió);
- tervezési jellemzők (a fémminőség kiválasztása, az alkatrészek közötti hézagok, az érdesség követelményei).
Fizikai és kémiai tulajdonságok
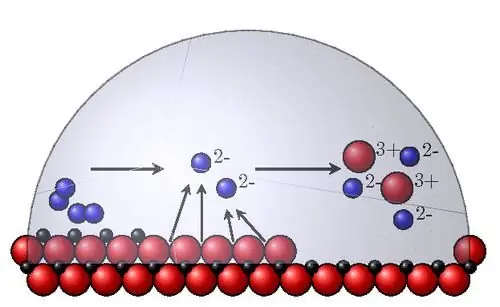
A legfontosabb belső korróziós tényezők a következők:
- Termodinamikai stabilitás. Vizes oldatokban történő meghatározásához referencia Pourbaix diagramokat használnak, amelyek abszcissza tengelye mentén a közeg pH-ját, az ordináta tengely mentén pedig a redoxpotenciált ábrázolják. A pozitív irányú potenciáleltolódás az anyag nagyobb stabilitását jelenti. Kísérletileg a fém normál egyensúlyi potenciáljaként határozzuk meg. A valóságban az anyagok különböző sebességgel korrodálnak.
- Egy atom helyzete a kémiai elemek periódusos rendszerében. A korrózióra leginkább érzékeny fémek az alkáli- és alkáliföldfémek. A korrózió sebessége az atomszám növekedésével csökken.
- Kristály szerkezet. Kétértelműen hat a pusztításra. A durvaszemcsés szerkezet önmagában nem vezet a korrózió fokozódásához, de kedvező a szemcsehatárok szemcseközi szelektív roncsolásának kialakulásához. A homogén fáziseloszlású fémek és ötvözetek egyenletesen, míg a nem egyenletes eloszlásúak fókuszmechanizmus szerint korrodálnak. A fázisok kölcsönös elrendezése az anód és a katód funkcióját tölti be agresszív környezetben.
- Az atomok energetikai inhomogenitása a kristályrácsban. A legnagyobb energiájú atomok az arcok sarkaiban helyezkednek elmikroegyenetlenségek és aktív oldódási központok a kémiai korrózió során. Ezért a fém alkatrészek gondos megmunkálása (csiszolás, polírozás, kikészítés) növeli a korrózióállóságot. Ezt a hatást az is magyarázza, hogy a sima felületeken sűrűbb és folytonosabb oxidfilmek képződnek.
A közepes savtartalom hatása
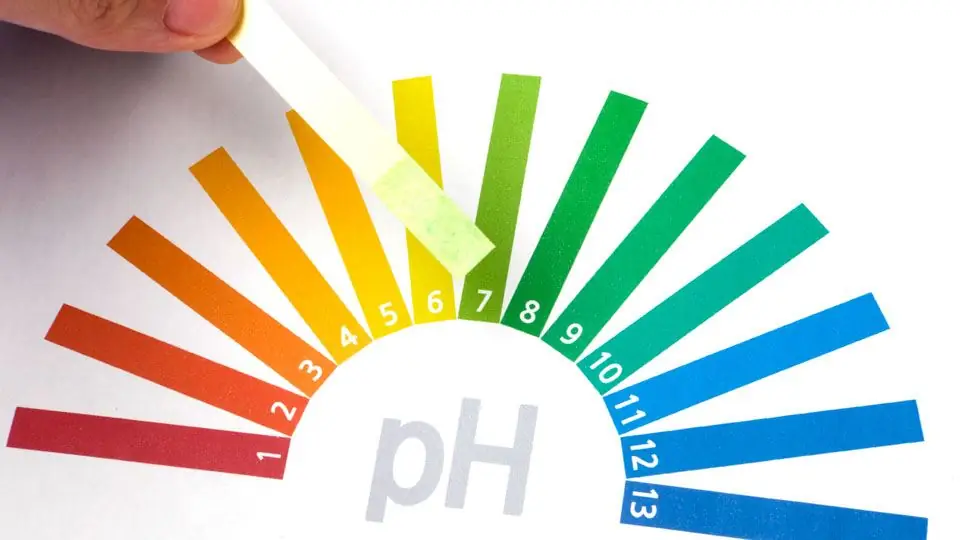
A kémiai korrózió folyamatában a hidrogénionok koncentrációja a következő pontokat érinti:
- korróziós termékek oldhatósága;
- védő oxidfilmek kialakítása;
- fémmegsemmisítési sebesség.
Ha a pH 4-10 egység (savas oldat) tartományban van, a vas korróziója a tárgy felületére való oxigén behatolás intenzitásától függ. Lúgos oldatokban a korrózió sebessége először a felület passzivációja miatt csökken, majd >13 pH-értéknél a védő oxidfilm feloldódása következtében nő.
Minden fémtípus esetében a pusztulás intenzitása az oldat savasságától függ. A nemesfémek (Pt, Ag, Au) savas környezetben ellenállnak a korróziónak. A Zn és az Al gyorsan elpusztul savakban és lúgokban egyaránt. A Ni és a Cd ellenáll a lúgoknak, de savakban könnyen korrodálnak.
Semleges oldatok összetétele és koncentrációja
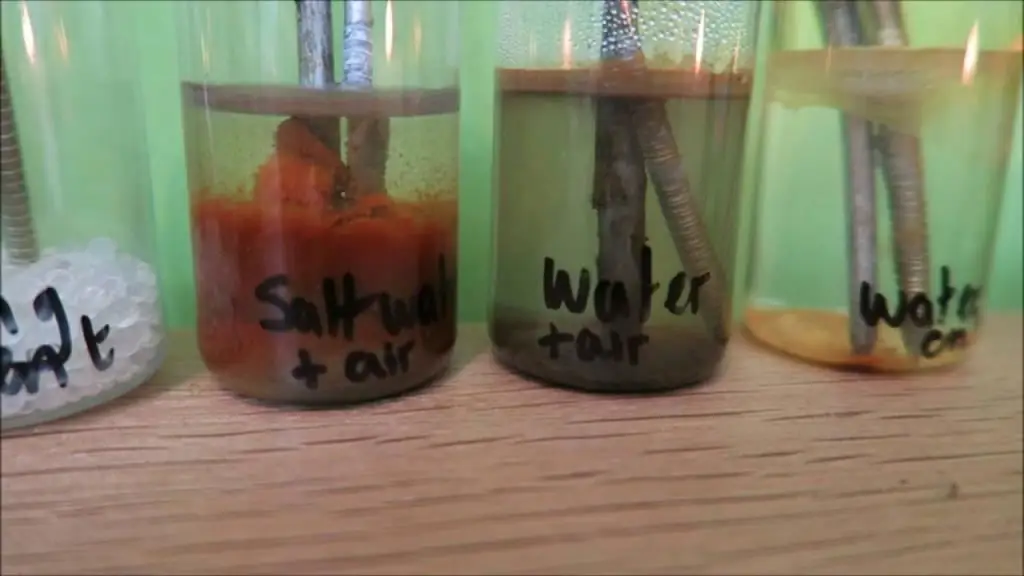
A semleges oldatokban a korrózió mértéke inkább a só tulajdonságaitól és koncentrációjától függ:
- A sók hidrolízise soránkorrozív környezetben ionok képződnek, amelyek a fémpusztulás aktivátoraként vagy késleltetőjeként (inhibitorként) működnek.
- A pH-t növelő vegyületek a pusztító folyamat sebességét is növelik (például szóda), a savasságot csökkentő vegyületek pedig csökkentik (ammónium-klorid).
- Kloridok és szulfátok jelenlétében az oldatban a roncsolás addig aktiválódik, amíg el nem ér egy bizonyos sókoncentrációt (amit az anódfolyamat klorid- és kénionok hatására felerősödő folyamata magyaráz), ill. majd fokozatosan csökken az oxigén oldhatóságának csökkenése miatt.
Bizonyos típusú sók képesek oldhatatlan filmréteget képezni (például vas-foszfát). Ez segít megvédeni a fémet a további károsodástól. Ezt a tulajdonságot rozsdamentesítő szerek alkalmazásakor használják.
Korróziógátlók
A korróziógátlók (vagy inhibitorok) különböznek a redox folyamatra kifejtett hatásmechanizmusukban:
- Anód. Nekik köszönhetően passzív film jön létre. Ebbe a csoportba tartoznak a kromátok és bikromátok, nitrátok és nitritek alapú vegyületek. Az utolsó típusú inhibitorokat az alkatrészek interoperációs védelmére használják. Az anódos korróziógátlók használatakor először meg kell határozni a minimális védőkoncentrációjukat, mivel kis mennyiségek hozzáadása a roncsolás sebességének növekedéséhez vezethet.
- Katód. Hatásmechanizmusuk az oxigénkoncentráció csökkenésén és ennek megfelelően a katódos folyamat lelassulásán alapul.
- Árnyékolás. Ezek az inhibitorok úgy izolálják a fémfelületet, hogy oldhatatlan vegyületeket képeznek, amelyek védőrétegként rakódnak le.
Az utolsó csoportba tartoznak a rozsda-semlegesítők, amelyeket az oxidok tisztítására is használnak. Általában foszforsavat tartalmaznak. Hatása alatt fémfoszfátozás következik be - az oldhatatlan foszfátokból álló erős védőréteg kialakulása. A semlegesítőket szórópisztollyal vagy hengerrel alkalmazzák. 25-30 perc elteltével a felület fehér-szürke színt kap. Miután a kompozíció megszáradt, festékeket és lakkokat kell felhordani.
Mechanikai hatás
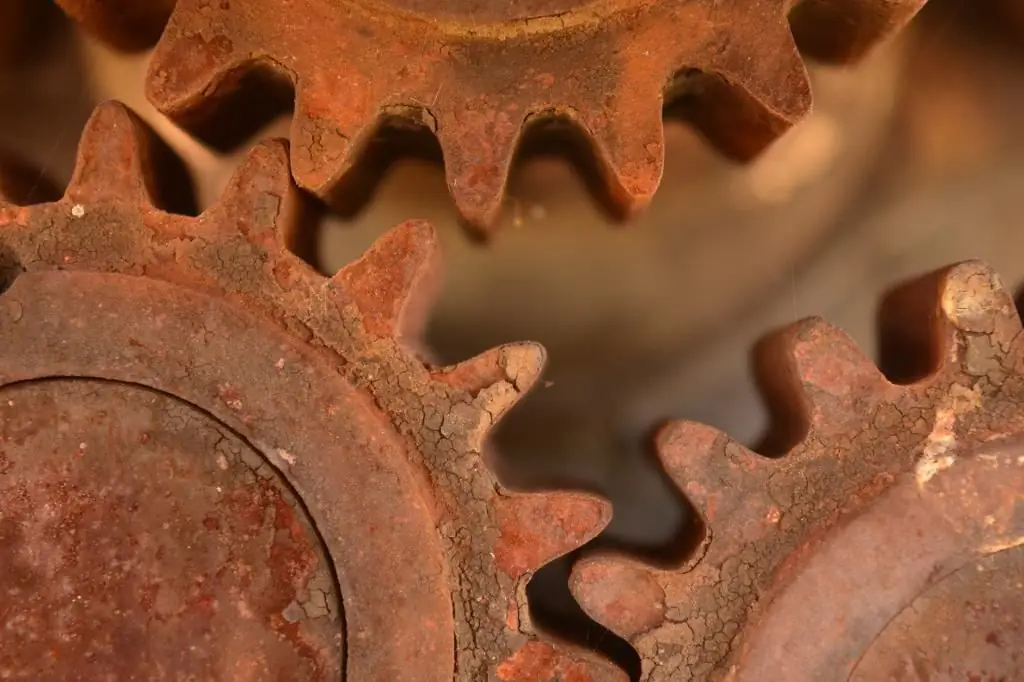
A korrózió növekedését agresszív környezetben a következő típusú mechanikai hatások segítik elő:
- Belső (formázás vagy hőkezelés során) és külső (külső terhelés hatására) feszültségek. Ennek eredményeként elektrokémiai inhomogenitás lép fel, az anyag termodinamikai stabilitása csökken, és korróziós repedés alakul ki. Különösen gyors a roncsolás húzó terhelések hatására (repedések keletkeznek merőleges síkban) oxidáló anionok, például NaCl jelenlétében. Az ilyen jellegű megsemmisítésnek kitett készülékek tipikus példái a gőzkazánok alkatrészei.
- Változó dinamikus hatás, vibráció (korróziós kifáradás). Intenzíven csökken a kifáradási határ, több mikrorepedés képződik, amelyek aztán egy nagyba egyesülnek. Számciklusok meghibásodása nagyobb mértékben függ a fémek és ötvözetek kémiai és fázisösszetételétől. A szivattyútengelyek, rugók, turbinalapátok és egyéb berendezések ki vannak téve az ilyen korróziónak.
- Alkatrészek súrlódása. A gyors korrózió az alkatrész felületén lévő védőfóliák mechanikai kopásának és a környezettel való kémiai kölcsönhatásnak köszönhető. Folyadékban a pusztulás sebessége kisebb, mint a levegőben.
- Kavitációs hatás. A kavitáció akkor fordul elő, ha a folyadékáramlás folytonossága megsérül a vákuumbuborékok képződése következtében, amelyek összeesnek és pulzáló hatást keltenek. Ennek eredményeként helyi jellegű mély károk keletkeznek. Az ilyen típusú korrózió gyakran megfigyelhető a vegyi berendezésekben.
Tervezési tényezők
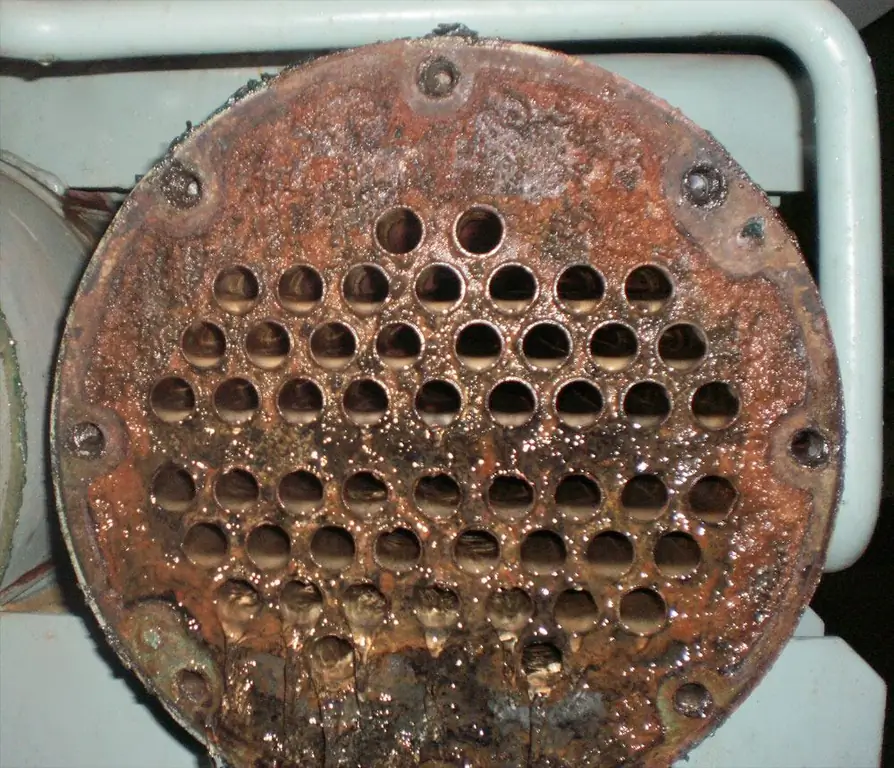
Agresszív körülmények között üzemelő elemek tervezésekor figyelembe kell venni, hogy a korrózió mértéke a következő esetekben nő:
- ha eltérő fémek érintkeznek egymással (minél nagyobb a köztük lévő elektródpotenciál különbsége, annál nagyobb az elektrokémiai roncsolási folyamat áramerőssége);
- mechanikus feszültségkoncentrátorok (hornyok, hornyok, lyukak és mások) jelenlétében;
- a megmunkált felület alacsony tisztaságával, mivel ez helyi rövidzárlatos galvanikus párokat eredményez;
- a berendezés egyes részeinek jelentős hőmérséklet-különbségével (termikus galvanikus cellák képződnek);
- stagnáló zónák (rések, rések) jelenlétében;
- alakításkormaradó feszültségek, különösen a hegesztett kötéseknél (ezek kiküszöbölésére hőkezelésről - izzításról gondoskodni kell).
Értékelési módszerek
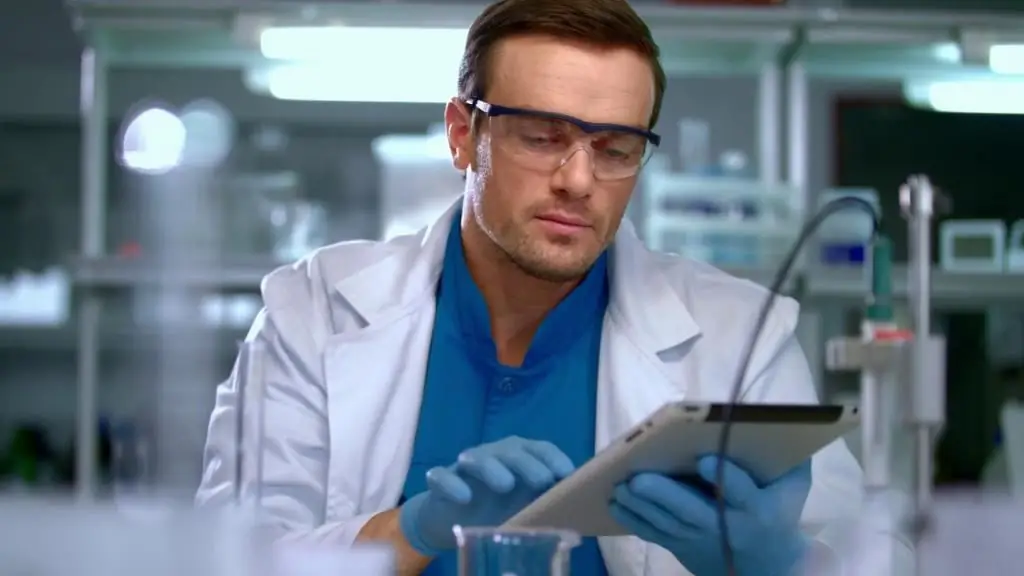
Többféle módszer létezik a fémek agresszív környezetben történő pusztulási sebességének felmérésére:
- Laboratórium - minták tesztelése mesterségesen szimulált körülmények között, közel a valósághoz. Előnyük, hogy lehetővé teszik a tanulmányozási idő csökkentését.
- Mező - természetes körülmények között tartva. Sokáig tartanak. Ennek a módszernek az az előnye, hogy információt nyerünk a fém tulajdonságairól a további működés körülményei között.
- Kész fémtárgyak helyszíni tesztelése természetes környezetben.